Flanges Manufacturing Process
- Categories:Product Information
- Author:Zhongran
- Source:Hebei Zhongran Pipeline Co., Ltd.
- Updated:2020-09-12
- Views:788
【Summary Description】
Flanges Manufacturing Process
【概要描述】
- Categories:Product Information
- Author:Zhongran
- Source:Hebei Zhongran Pipeline Co., Ltd.
- Updated:2020-09-12
- Views:788
Flanges Manufacturing Process
Our manufacturing process is highly sophisticated and is divided into various departments supervised by experienced industry experts. We use only quality raw materials that are procured from only established and reliable vendors. We have adopted rigorous quality control practices and procedures to ensure the production of only quality products matching industry standards and parameters.
Casting flange is a commonly used flange technology, which has the advantages of high production efficiency and low production cost, and is suitable for medium and low pressure pipelines. Forged pipes are recommended for pipes operating at high pressures.
The casting flange is made of iron filings. After the iron mill is melted, the molten iron is poured into the mold, cooled, and processed. Some processing procedures are to pour the molten iron into the mold and heat it in the forging after molding. A form of processing.
Our product range include all types of flanges such as MS Flange ( Mild Steel ) , Raised face flange , Weld neck flange, Bellow Flange , and Flanges according to custom requirement.
Requirements are valid for normal situation, in special you have to contact us to introduce.
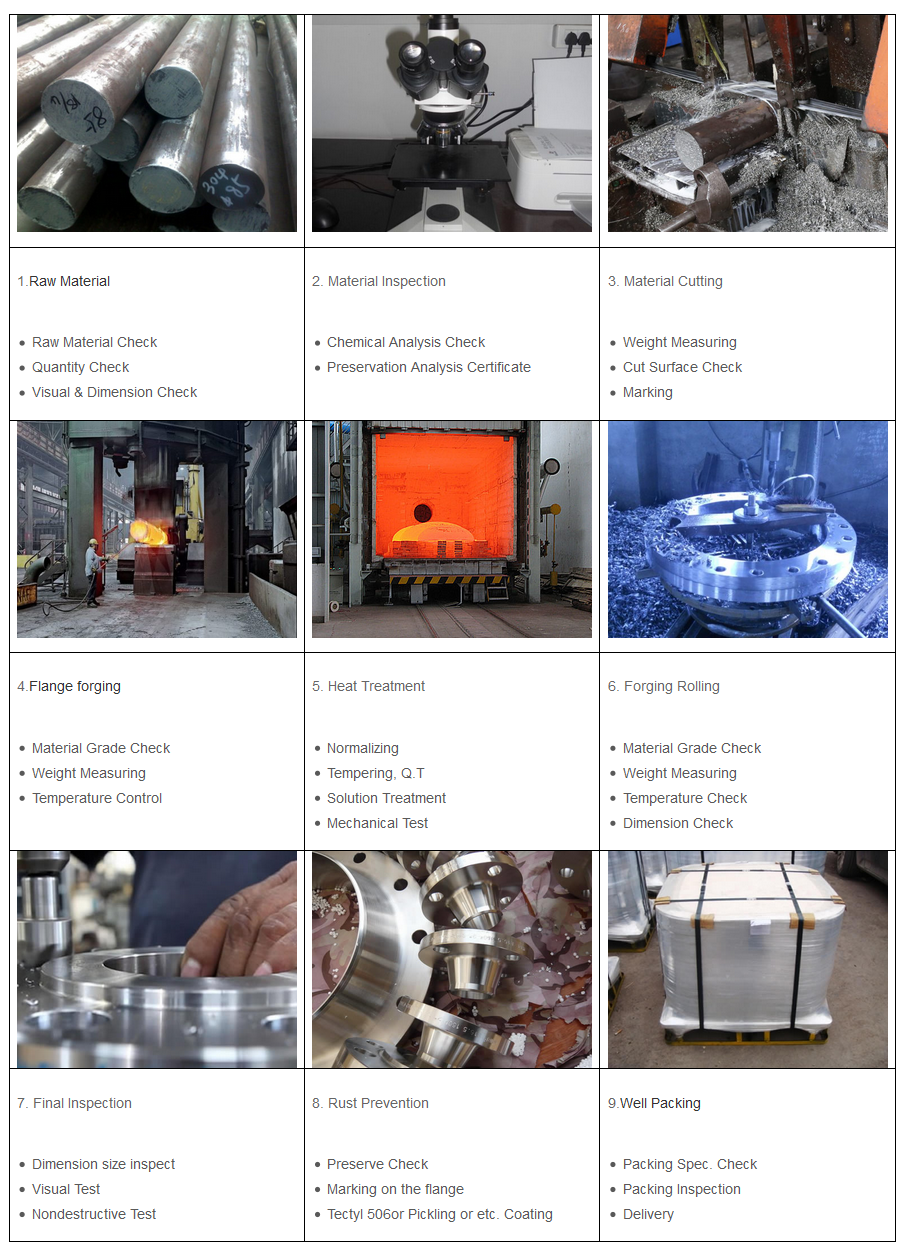
Raw Materials:
The usual materials of flanges include stainless steel, carbon steel, aluminum and plastic.
Beginning with this process,the system controls the quality of all incoming materials as per the raw material test certificate of the material. Mild Steel Flanges ( MS ) are of premium quality that ensures high durability, strength and resistivity to varied non-supporting conditions. Also, checking in each size for chemical and physical properties of these materials at Government approved laboratory.
Flange materials acc. to ASTM
Dimensions from carbon steel and stainless steel flanges are defined in the ASME B16.5 standard. The material qualities for these flanges are defined in the ASTM standards.
The Packing Works for Steel Flanges
Steel flanges must be packed with seaworthy packing method then delivery to customers, usually the packing way include wooden box, wooden pallet, iron & steel cage, iron & steel pallet etc. Because of the normal wooden boxes or wooden pallets have to do fumigation treatment, we usually use plywood pallet or plywood case or box to pack steel flanges without fumigation treatment. Whatever plywood or iron & steel packing way, they must be seaworthy, strong, waterproof and easy for loading and unloading.
Marking on the flange
Shipping mark stick to outside of package. Following shall be marked on flange body
- Manufacturer logo
- ASTM material code
- Material Grade
- Service rating (Pressure-temperature Class))
- Size
- Thickness (Schedule)
- Heat No
- Special marking if any QT (Quenched and tempered) or W (Repair by welding)
Dispatch:
The final process of dispatch is the most tedious of all , and heavy duty cranes are used for it. With the help of our extensive delivery chain we can ensure time critical deliveries at the behest of our esteemed clients. We are indeed privileged to be able to serve and live upto their expectations and occupy unparalleled postion of Flange makers in China.
The production process of forged flange:
Free forging
The free forging productivity is low, the machining allowance is large, but the tool is simple and the versatility is large, so it is widely used for forging a single piece and a small batch of forgings with a simple shape. Free forging equipment includes air hammer, steam-air hammer and hydraulic press, which are suitable for the production of small, medium and large forgings. Flange processing manufacturers look for Titanium machinery. Die forging has high productivity, simple operation, and easy mechanization and automation. The die forgings have high dimensional accuracy, small machining allowance, and the fiber structure distribution of the forgings is more reasonable, which can further improve the service life of the parts.
The basic process of free forging: When free forging, the shape of the forging is gradually forged by some basic deformation process. The basic processes of free forging are upsetting, lengthening, punching, bending and cutting.
- Upsetting: Upsetting is an operation process in which the raw material is forged in the axial direction to reduce its height and increase the cross section. This procedure is commonly used for forging gear blanks and other disc-shaped forgings. The ups and downs are divided into two types: all upsetting and partial forging.
- Pulling length: Pulling length is a forging process that increases the length of the blank and reduces the section. It is usually used to produce shaft blanks, such as lathe spindles and connecting rods.
- Punching: a forging process in which a punch punches a through hole or a through hole without using a punch.
- Bending: a forging process of bending a billet into a certain angle or shape.
- Torsion: A forging process that rotates a portion of a blank relative to another portion at a certain angle.
- Cutting: the forging process of dividing the blank or cutting the material.
Die forging
The die forging is collectively referred to as model forging, and the heated blank is placed in a forging die fixed to the die forging device to be forged.
- The basic process of die forging The process of die forging: cutting, heating, pre-forging, final forging, punching, trimming, quenching and tempering, shot peening. Commonly used processes are upsetting, lengthening, bending, punching, and forming.
- Commonly used die forging equipment Common die forging equipment has die forging hammer, hot die forging press, flat forging machine and friction press.
Generally speaking, forged flanges are of better quality, generally produced by die forging, with fine crystal structure and high strength, of course, the price is also more expensive.
Both the cast flange and the forged flange are common methods of manufacturing flanges. See the strength requirements of the parts to be used. If the requirements are not high, you can also use the turning flange.
Comparison of cast flanges and forged flanges
The difference between the forged flange and the cast and forged flange is that the forged flange is a process for producing a production flange which is developed on the basis of the cast flange. The forged flange has higher strength than the cast flange. The quality is relatively good, the price will not increase a lot. Generally, the low-quality pipes will be connected by casting flanges. The high-quality pipes will be purchased with forged flanges. The quality of the forged flanges is better. In the quality pipeline, it is not useful for the low-quality pipeline to be able to exert sufficient performance. Casting flanges can only be used up to 16Kg, and are normally used in 10Kg or 6Kg pipes. Except for pressure requirements, the temperature should not be too high or too low. Generally there is no specification, but it is recommended to use forged flanges for important pipes. For example, some places with high temperature difference or vibration of the pipe may cause breakage, cracking, water leakage, etc. due to poor quality of the cast flange.
- The flange is cast, the shape of the blank is accurate, the processing volume is small, and the cost is low, but there are casting defects (pores, cracks, inclusions); the internal flow of the casting is poor (if it is a cutting part, the streamline type is worse);
- Forged flanges generally have lower carbon content than cast flanges and are less prone to rust. Forgings have better streamlined shape, denser structure and better mechanical properties than cast flanges;
- If the forging process is improper, the grain will be large or uneven, and the hardening crack will occur. The forging is higher than the casting flange;
- Forged flanges can withstand higher shear and tensile forces than cast flanges;
- The advantage of the cast flange is that it can produce a more complicated shape and the cost is relatively low;
- The advantage of the forged flange is that the internal structure is uniform, and there are no harmful defects such as pores and inclusions in the casting;
Different from the production process, the difference between the cast flange and the forged flange, such as the centrifugal flange, is one of the cast flanges.
The centrifugal flange belongs to the production flange of precision casting method. This kind of casting is much thinner than ordinary sand casting structure, and the quality is improved a lot. It is not easy to have problems such as loose structure, pores and trachoma.
First of all, we need to understand how the centrifugal flange is produced and processed by centrifugal casting to make a flat welding flange. The product is characterized by the following process steps:
The selected raw material steel is smelted in an intermediate frequency electric furnace to make the molten steel temperature reach 1600-1700 ° C;
Preheat the metal mold to 800-900 ° C to maintain a constant temperature;
Start the centrifuge, and inject the molten steel in step 1 into the metal mold after preheating in step 2;
The casting is naturally cooled to 800-900 ° C for 1-10 minutes;
Cool down to near normal temperature with water and demould remove the casting.
Cutting flange
On the middle plate, the disk with the inner diameter and the inner diameter of the flange with the processing amount is directly cut out, and the bolt hole and the water line are processed. The flange thus produced is called a cut flange, and the maximum diameter of such a flange is limited to the width of the middle plate.
Coiled flange
The process of cutting the strips with the middle plate and then rolling them into a circle is called rolling, and is used for the production of some large flanges. After the winding is successful, the welding is carried out, and then the flattening is performed, and then the process of the water line and the bolt hole is processed.
The flange is the part of the shaft and the shaft that is connected to each other for the connection between the ends of the pipe. It is also used for the flange on the inlet and outlet of the device for the connection between two devices, such as the flange of the reducer. A flange connection or a flange joint refers to a detachable connection in which a flange, a gasket and a bolt are connected to each other as a combined sealing structure. Choose to process a variety of high-quality flanges to identify Titanium machinery, pipe flanges refer to the flanges used in piping in pipeline installations, used on the equipment to refer to the inlet and outlet flanges of the equipment. There are holes in the flange, and the bolts make the two flanges tightly connected. The flanges are sealed with gaskets. Flange threaded connection (threaded connection) flange, welded flange and clip flange.
Flange connection is an important connection method for pipeline construction. The flange connection is easy to use and can withstand large pressures. Flange connections are widely used in industrial piping. In the home, the pipe diameter is small and low pressure, and the flange connection is not visible. If you are in a boiler room or production site, there are flanged pipes and equipment everywhere.
Basic requirements for Material and Fitting
Requirements are valid for normal case, in special case you have to contact the technical department.
掃二維碼用手機看
- Telphone- 0317-6165555 6689999
- E-mail- 798758696@qq.com
- Address- Yanshan County Industrial Park, Cangzhou City, Hebei Province
- Telphone- 0317-6165555 6689999
- E-mail- 798758696@qq.com
- Address- Yanshan County Industrial Park, Cangzhou City, Hebei Province